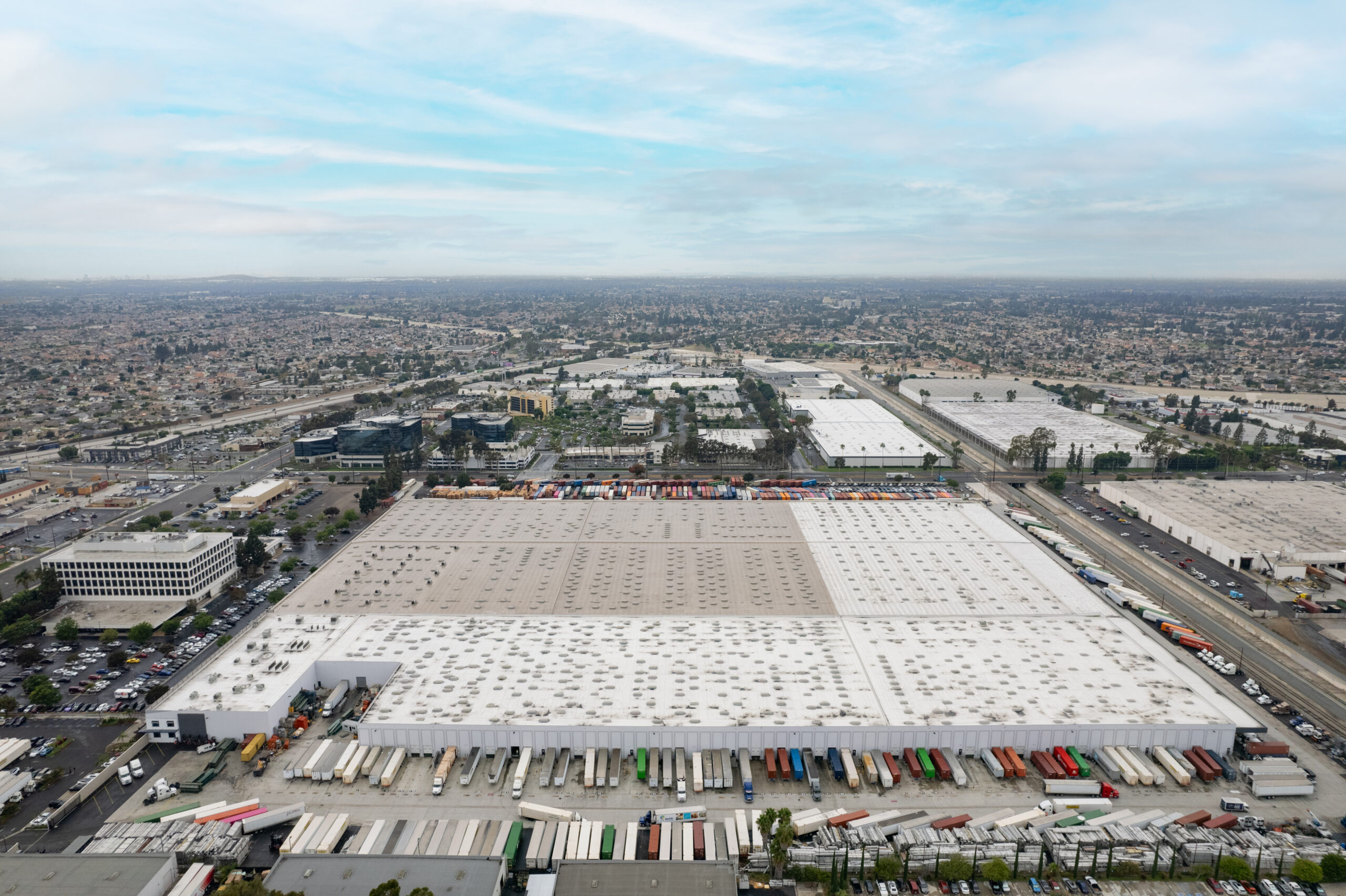
How to Choose the Most Effective Logistics Site in the U.S
19 May, 2025
By xavier
Share to
Selecting the optimal logistics site in the United States is a critical decision. Companies aim to enhance efficiency, reduce costs, and improve service levels. The key is to find a location that fits your business goals and how you operate. You must also consider important things like transportation, proximity to customers, and whether there are enough workers.
This guide examines what makes a top U.S. logistics site and how smart firms use flexible warehouse space. From temporary warehouse space to hybrid office and warehouse setups, to maximize performance and minimize costs.
Why Location Still Wins in Logistics
We’ve all heard the saying: “Location, location, location.” In logistics, this is more than just a mantra—it’s a measurable advantage.
A strategically placed distribution center can reduce transportation costs by 10-20% and slash delivery times. That’s why leading companies—from Amazon to smaller 3PLs—place warehouse units near urban cores and transport arteries.
The rise of regional fulfillment centers is also changing the game. Businesses are creating smaller nodes near customers, improving delivery SLAs.
📊 Industry research shows that same-day delivery options can drastically reduce cart abandonment and increase satisfaction, with 40% of consumers abandoning carts if same-day delivery isn’t available. (Metrobi)
Key Factors in Logistics Site Selection
Here are the strategic considerations every logistics team must evaluate:
1. Proximity to Transportation Infrastructure
Being close to major highways, ports, rail lines, and air cargo hubs can drastically reduce transit times and fuel costs.
Examples:
- Inland Empire, CA – Access to Ports of LA and Long Beach.
- Dallas-Fort Worth, TX – Central location with interstate access.
- Memphis, TN – FedEx hub with world-class air cargo facilities.
2. Access to Population Centers
The closer you are to urban density, the faster your last-mile delivery. Especially important for e-commerce and B2C fulfillment.
3. Labor Availability and Cost
An ideal site balances skilled workforce availability (warehouse workers, forklift operators, drivers) with sustainable wage levels.
Example:
- Labor costs in California remain high, while Tennessee or Ohio offer significant savings with comparable talent pools.
4. Tax & Incentive Structures
Many states offer tax incentives, grants, or zoning allowances to attract logistics businesses. These programs can reduce your capital outlay and operating costs significantly.
5. Climate, Risk, and Resilience
Avoid areas prone to hurricanes, wildfires, or flooding, especially for mission-critical fulfillment centers.
Also assess supply chain resilience: Can the region sustain operations during major disruptions?
6. Utility Access and Industrial Zoning
Ensure the site supports high-load electricity, water, and broadband. Also, check zoning compliance for office and warehouse operations.
7. Speed to Market and SLA Expectations
Choose locations that align with your shipping timelines. Some 3PLs and e-commerce brands now guarantee same-day delivery—proximity to metro areas is key.
Hotspot Comparison: Best Logistics Hubs in the U.S.
Region | Strengths | Use Case |
---|---|---|
Inland Empire, CA | Port access, dense population | West Coast fulfillment |
Dallas-Fort Worth | Central U.S. location, road connectivity | National distribution |
Chicago, IL | Rail/air access, skilled labor | Midwest hub |
Memphis, TN | FedEx air cargo, incentives | Express shipping |
Atlanta, GA | Airport + I-75 corridor access | Southeastern gateway |
Case Study: UNIS and Strategic Site Selection Success
UNIS, a national 3PL provider, needed to expand its fulfillment operations across key U.S. markets. Therefore, it focused on logistics site selection as a core strategic move. Customers increasingly demanded next-day delivery. Because of this, UNIS prioritized warehouse units in population-dense areas with access to major highways and intermodal transport.
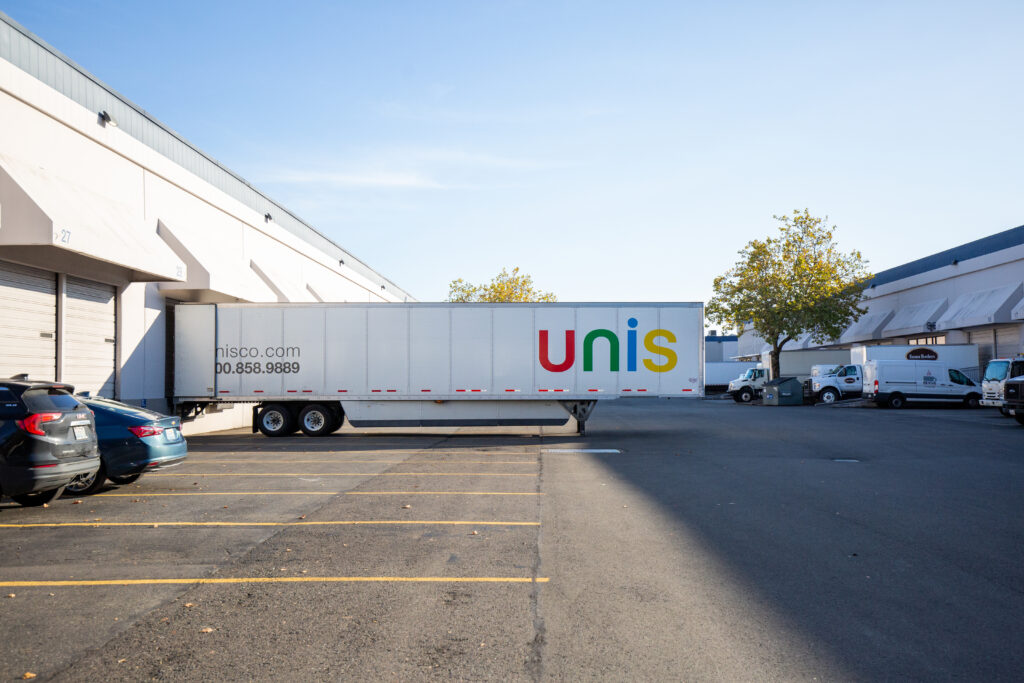
By partnering with flexible providers like Cubework, UNIS secured short-term warehouse space. This was in regions like Southern California and Dallas–Fort Worth, two competitive logistics markets with limited supply. These sites offered immediate access to large warehouse bays, office/warehouse combinations, and the necessary utilities for quick growth.
The result was clear: faster delivery, lower last-mile costs, and happier customers. This shows that choosing the right logistics site is a strategic move for growth, not just real estate.
Flexible Industrial Real Estate: A Modern Requirement
In a market that demands agility, long leases are a liability. More companies are turning to:
- Temporary warehouse space for seasonal overflow
- Warehouse bays to segment operations or sublet capacity
- Office and warehouse combinations that support hybrid logistics teams
- Warehouse units that can expand or contract as needed
📦 With flexible industrial real estate, you’re not just renting space but buying time and adaptability.
Mistakes to Avoid When Choosing a Logistics Site
- Focusing only on rent without factoring in transport costs
- Without considering the availability and competitive cost of labor.
- Choosing without zoning approval or power access
- Failing to assess delivery SLA requirements accurately.
- Overcommitting to long-term leases in unstable markets
The Role of Technology in Site Evaluation
Data drives modern logistics site selection. Technologies like:
- GIS mapping for route optimization
- Labor market analytics
- Real-time inventory modeling
- Platforms like Colliers’ site intelligence tools
These tools help companies make informed decisions, balancing cost, risk, and performance.
Explore Colliers’ logistics real estate insight
Final Checklist: What to Evaluate Before Signing a Lease
✅ Proximity to transport infrastructure
✅ Population access for delivery
✅ Labor cost and availability
✅ State/local tax incentives
✅ Zoning and utility readiness
✅ Physical warehouse room layout
✅ SLA alignment with business model
✅ Flexibility of lease terms
Choose Wisely, Move Quickly
The best place for your logistics balances cost, how easy it is to get to, how reliable it is, and how flexible it is. If you think carefully about where to put your logistics, you can deliver faster and save money.
FAQ
1. What makes a location ideal for warehousing space in the U.S.?
Easy access to transportation—highways, ports, and airports—is key for a great logistics location. It should also be near major population centers for last-mile delivery. A good supply of workers and appropriate industrial zoning are important, too. Finally, flexible leasing, such as short-term warehouse spaces, adds to its adaptability and cost-effectiveness.
2. How do office and warehouse combinations benefit logistics operations?
Office and warehouse combinations enable centralized operations, allowing inventory management, fulfillment, and administrative functions to occur under one roof. This improves communication and workflows, especially for 3PLs and e-commerce needing real-time coordination.
3. Why is temporary warehouse space important for growing businesses?
Temporary warehouse space provides flexibility for businesses experiencing seasonal demand, market testing, or rapid expansion. This lets companies grow without long leases, which helps manage cash and reduce overhead when growth is uncertain.
4. How do I evaluate whether a warehouse unit suits my needs?
Consider size (square footage), number of warehouse bays, ceiling height, loading dock access, utility availability, zoning regulations, and potential for office integration. For e-commerce or distribution companies, evaluate how the space supports delivery timelines and inventory management systems.
Connect with Cubework
Let us help you find the ideal warehouse unit with office space, loading bays, and short-term leasing options to keep you agile. Explore available spaces near you. Talk to us or consult our expert logistics real estate team today. Contact us at 888-599-7809 or via email at info@cubework.com.